Air Blowing
Air blow cleaning services are a safe and cost effective method for cleaning all types of piping systems. Typically, air blowing pre commissioning is performed after the completion of hydrotesting. Air blowing will remove loose rust, sand, dirt, and construction debris. By performing an air blowing pipe cleaning before the startup of new systems, it can be ensured that no debris or contaminants will inadvertently block valves, damage equipment, or foul the process.
There are several different configurations used for air blowing depending on the design of the piping system being cleaned. Continuous air blows are effective for small diameter pipes. Rupture air blows, also called decompression air blows, are used on large diameter piping and can be effective on very long runs of piping. A third type of air blow cleaning using a pressure vessel as a reservoir can by employed for short runs of large diameter piping.
To ensure cleanliness RIG will calculate cleaning force ratios for all engineered air blows along with associated air pressures and cleaning velocities. Similar to targeting during a steam blow an air blow can also have a target inserted at the exit point to prove system cleanliness.
Proper engineering of air blows is essential to their success in cleaning the system. The RIG team can recommend the best air blowing pipe cleaning methods for your application. Learn more about our air blowing service below or contact us to get a quote.
800-770-4510 (Domestic)
+1 281-339-5751 (International)
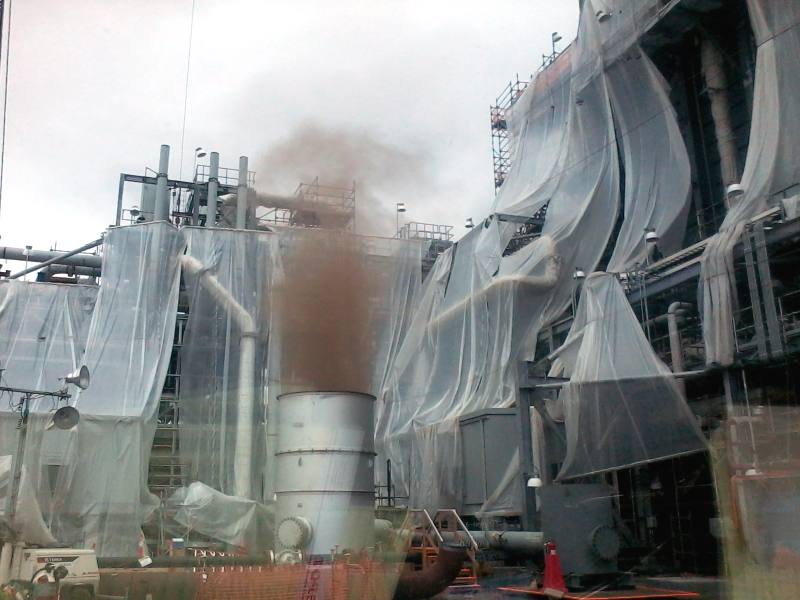
Typical Air Blowing Pipe Cleaning Procedure
For Effective Air Blow Cleaning
Our team of engineers will help to develop a custom procedure for your situation. Typically, an air blow project progresses as follows:
- Systems to be cleaned are identified on the P&IDs and cleaning paths are marked. Injection points, exits points, valve positions, and equipment to be removed are detailed on the drawings.
- Cleaning force ratios, air pressures, and cleaning velocities are calculated for each of the air blows.
- Connection point details are recorded, and a bill of materials of temporary adaptors and equipment is created.
- The air blowing equipment including air compressors, air dryers, silencers, hoses, and temporary connection fittings is shipped to site.
- In the field the RIG Supervisor will walk down the system to be air blown following the procedure prepared by the engineer. Connection points, items to be removed, and access to the piping will be noted.
- The RIG crew will verify that the piping system is isolated. The temporary air blowing equipment will then be connected to the system.
- A safety briefing will be held and workers in the area will be notified that air blowing activities are about to start.
- The RIG crew will then pressurize the piping systems and release the air at the exit point. Contamination levels will be noted and the relevant parties (RIG, client, owner) will witness the cleaning.
- If targets are required, they will be inserted into the exit piping via a target inserter.
- Once the system is accepted as clean the temporary equipment will be removed from the piping and the system will be reinstated to await startup.
Husky Lima OH – New Hydro Plant- The RIG team performed chemical cleaning on the reformer, air blowing of the process lines and continuous steam blows of the header and users.
DTE Cogeneration to Solvay Marietta, Ohio. RIG performed chemical cleaning of the boilers, gas line air blows and steam blows.
Valero Cogen Wilmington CA – RIG performed citric acid chemical cleaning of the HRSG, gas line air blow to the duct burners and combustion turbine. Oil flushing of the combustion turbine and Kobelco compressor. Steam blows to the header.
What is air blowing?
Air blowing is an industrial plant service that uses dry oil-free compressed air to clean piping of debris and contaminants. It will remove construction debris, liquids, and semi adherent material, and safely transport the removed items out of the system. This method allows for quick cleaning of piping systems without the need for disposal of large volumes of liquid cleaning solutions.
Should I hydrolaze before air blowing pipe cleaning?
Hydrolazing, sometimes also called aqualazing or hydromilling, is a pipe cleaning service that can significantly enhance the results of steam and air blowing. This high-pressure water jetting process is effective at removing mill scale, construction debris, and process deposits. Air blowing will not remove all mill scale from the internal pipe wall. For systems that require a high degree of cleanliness the combination of hydrolazing followed by air blowing can yield excellent results without the generation of large volumes of chemical cleaning waste.
When should I use air blowing vs. steam blowing?
Air blowing pre commissioning works well in combination with chemical cleaning. The air blows will remove all loose debris. The chemical cleaning solution will then dissolve the remaining mill scale. Air blowing puts less direct stress on your system than steam blowing does, so if a chemical clean will remove the contaminants, it is easier on your system to combine it with air blowing.
Husky Lima OH – New Hydro Plant- The RIG team performed chemical cleaning on the reformer, air blowing of the process lines and continuous steam blows of the header and users.
DTE Cogeneration to Solvay Marietta, Ohio. RIG performed chemical cleaning of the boilers, gas line air blows and steam blows.
Valero Cogen Wilmington CA – RIG performed citric acid chemical cleaning of the HRSG, gas line air blow to the duct burners and combustion turbine. Oil flushing of the combustion turbine and Kobelco compressor. Steam blows to the header.
Typical Air Blowing Procedure
Our team of engineers will help to develop a custom procedure for your situation. Typically, an air blow project progresses as follows:
- Systems to be cleaned are identified on the P&IDs and cleaning paths are marked. Injection points, exits points, valve positions, and equipment to be removed are detailed on the drawings.
- Cleaning force ratios, air pressures, and cleaning velocities are calculated for each of the air blows.
- Connection point details are recorded, and a bill of materials of temporary adaptors and equipment is created.
- The air blowing equipment including air compressors, air dryers, silencers, hoses, and temporary connection fittings is shipped to site.
- In the field the RIG Supervisor will walk down the system to be air blown following the procedure prepared by the engineer. Connection points, items to be removed, and access to the piping will be noted.
- The RIG crew will verify that the piping system is isolated. The temporary air blowing equipment will then be connected to the system.
- A safety briefing will be held and workers in the area will be notified that air blowing activities are about to start.
- The RIG crew will then pressurize the piping systems and release the air at the exit point. Contamination levels will be noted and the relevant parties (RIG, client, owner) will witness the cleaning.
- If targets are required, they will be inserted into the exit piping via a target inserter.
- Once the system is accepted as clean the temporary equipment will be removed from the piping and the system will be reinstated to await startup.
What is air blowing?
Air blowing is an industrial plant service that uses dry oil-free compressed air to clean piping of debris and contaminants. It will remove construction debris, liquids, and semi adherent material, and safely transport the removed items out of the system. This method allows for quick cleaning of piping systems without the need for disposal of large volumes of liquid cleaning solutions.
Should I hydrolaze before air blowing?
Hydrolazing, sometimes also called aqualazing or hydromilling, is a pipe cleaning service that can significantly enhance the results of steam and air blowing. This high-pressure water jetting process is effective at removing mill scale, construction debris, and process deposits. Air blowing will not remove all mill scale from the internal pipe wall. For systems that require a high degree of cleanliness the combination of hydrolazing followed by air blowing can yield excellent results without the generation of large volumes of chemical cleaning waste.
When should I use air blowing vs. steam blowing?
Air blowing works well in combination with chemical cleaning. The air blows will remove all loose debris. The chemical cleaning solution will then dissolve the remaining mill scale. Air blowing puts less direct stress on your system than steam blowing does, so if a chemical clean will remove the contaminants, it is easier on your system to combine it with air blowing.