Steam Blowing
Rust, dirt, mill scale, and construction debris present before startup in boilers, turbines, pipelines, superheaters, and other equipment are the number one cause of downtime for new systems. Steam blowing is an effective and safe method for ensuring your systems are free of contaminants before startup. High velocity steam is blown through the systems at engineered velocities and pressures and then vented to atmosphere via temporary piping just before a critical component like a steam turbine.
Steam blowing is a critical activity during the commissioning of a new steam system. Any steam system feeding a steam turbine must be steam blown to remove debris that would damage the steam turbine blades. Steam blowing is also employed to clean process steam lines and utility steam systems.
Learn more about our steam blow capabilities below or reach out to RIG’s experienced team for a quote.
800-770-4510 (Domestic)
+1 281-339-5751 (International)
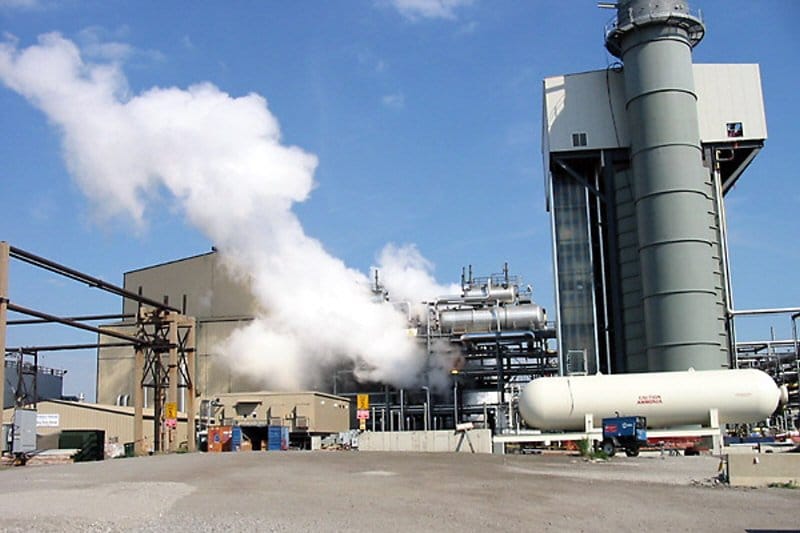
OCI Methanol Beaumont: Plant restart and upgrade. Continuous steam blows, oil flushing, line blowing and chemical cleaning.
Longview Power Station Maidsville, WV – New Coal fired power plant – RIG performed chemical cleaning of the Boiler and Pre-boiler piping systems and performed impulse steam blows.
Jaguar Coal Fired Power Plant – 2 blocks Coal Fired Boilers- Performed chemical cleaning of the boilers. Hydrolazing on Steam, CCW, BFW and Condensate piping. Impulse steam blows.
Air Products Tees Valley Waste to Energy UK – RIG performed chemical cleaning of the HRSG’s, Hydrolazing of the Piping, Oil flushing of the CT’s / STG and steam blows of the headers and to the STG.
Hines Power Block Progress Energy Lakeland, FL – Chemical Plant Commissioning Project- New Combined Cycle project- Nooter Eriksen HRSG’s, Westinghouse CT’s and STG-Performed citric acid chemical cleaning, hydrolazing of all steam piping, air blows on Block 2 and continuous steam blows on Block 3.
RIG’s Steam Blowing Procedure
A typical steam blowing project with RIG progresses as follows:
- During an initial call, we extract critical project specifications and key information from you
- One of our engineers performs a site walk down to thoroughly plan the steam blowing procedure including the number of exit points, type of blow, temporary piping requirements, and other engineered features of your specific system.
- Any recommended pre-blowing services such as chemical cleaning, hydraulic line testing, and plate checks are performed.
- Our team takes full responsibility for the blow, shipping all necessary equipment and running the job on-site. A typical steam blow follows one of two methods:
- Impulse / puffing steam blows
- Boiler pressure is slowly raised to a pre-calculated pressure level and firing rate is increased.
- The water level in the drum is brought slightly above normal because during blowing it will drop significantly.
- Impulse / puffing steam blows
- A low-pressure verification blow is performed to ensure proper system setup for temporary piping and anchors.
- Temporary piping is used from a temporary steam turbine exit with water injection along the pipe to help quench and reduce the volume of steam before it reaches the steam exhauster/silencer. The quenching reduces the noise level.
- Temporary valve is opened to blow through the superheater, main steam pipe, and temporary pipe.
- Additional rounds of high-pressure ‘puffs’ are sent through the system. Steam blows are conducted without target plates until steam color becomes clear. Then preliminary target or impact plates are placed to capture particles going with the steam. RIG impulse steam blow uses the latest in fast opening hydraulic actuated valves that are hard surface coated to withstand debris and repeated opening and closing.
- While blowing, the boiler fire is put out and pressure is dropped, ensuring proper temperature differential to dislodge any adhering material.
- Steam blowing valve is closed and boiler is started.
- Final target plate of turbine blade is placed once preliminary target plate is in acceptable form.
- Blowing continues until indentations are acceptable as per turbine manufacturer guidelines.
- After mainstream line is complete, other stages are done in the similar fashion.
- Low pressure continuous blowing
- The process for continuous blowing is similar to the impulse blow method, but steam is produced by the boiler or heat recovery system generator and then allowed to escape through a temporary exit into piping.
- Additionally, pressure and temperature is continuously maintained during this method, which is easier on plant equipment
- The drawback to this method is that it is not quite as effective as the impulse method at removing debris because piping does not expand and contract as much, which can be key to dislodging some contaminants.
- Once the appropriate steam blow has been performed, we verify cleanliness levels with a visual inspection
- Temporary set-ups are then dis-assembled and full project documentation is turned over to you
Our team of pre-commissioning service experts ensures a safe and effective steam blow at your facility by creating a thorough work plan and documenting all potential hazards before the blow begins. We pre-plan, monitor, and track every detail to make sure no unnecessary thermal stress or pressure is used on your system, boiler, or sensitive equipment.
What is steam blowing?
It is the blowing of steam through piping to remove debris from the pipe, cleaning steam lines to a steam turbine, cleaning plant expansion lines, or new installs. As the definition says, to steam blow a pipe requires steam to blow through the pipe. This pipe can be attached to a boiler or heat recovery steam generator, and the other end of the pipe can be attached to a steam turbine.
Are there different types of steam blowing?
Yes, there are two main types of steam blow.
Continuous low-pressure steam blow: Steam is produced by the boiler or heat recovery steam generator and sent down the steam line piping at high velocity. The low-pressure method allows for a continuous steam pressure and temperature on the permanent plant equipment. The required steam blow is pre-calculated to use about 45 to 55% of the maximum design steam flow but at a low pressure. The low pressure upstream in the piping will be the back pressure of the permanent piping plus the temporary piping to the silencer. This method relies on high velocity, low density steam to clean the piping as opposed to the steam during operation which is low velocity, high density, and high pressure.
Impulse steam blows: The accepted method for a steam blow per NEMA 23 and NEMA 24 is an impulse blow where steam is pressurized in the boiler and released rapidly by opening a block valve. A break out point at the steam turbine is established and a quick opening valve is attached to this break out and a short piece of pipe is attached to vent the steam in a safe direction.
What types of silencers do you use?
Dry silencers are utilized where no personnel will come in contact with the temporary piping, the temporary piping is at full exit temperature, this will require the craft people to be quarantined from the area where the steam piping will be routed.
Water injection type silencers do require injection of water down stream of the permanent piping tie-in, as a result the temporary piping temperature is reduced dramatically. This is the safest application for congested work areas that will contain craft personnel.
How long does a steam blow procedure take?
The length of a steam blow varies depending on the specifics of the system being cleaned (pipe lengths, number of exit points, etc), however an average steam blowing project can take around 2 weeks. To shorten this timeline, hydrolazing before a steam blow can shave 5-8 days off the steam blow.
Continuous steam blows can usually be completed much faster than an impulse steam blow. An impulse steam blow takes many valve cycles to exhaust the steam at a good cleaning force ratio for only short sections at a time, whereas, during a continuous steam blow the steam is always flowing and the cleaning force ratio becomes greater down the line as the pressure drops towards the exit.
What regulations do you follow during steam blows?
Generally when the piping is attached to a steam turbine the steam turbine manufacturer has already developed a guideline as to how this piping must be steam blown. There are several general methods already established to complete this and of these NEMA 23 and NEMA 24 are two of the guidelines generally referenced. These are general guidelines and Section 8 of each NEMA procedure is identical as to method and purpose of the steam blow.
How do you reduce noise and high temperatures during steam blowing?
One basic precaution includes using dry silencers that don’t require water injection to reduce noise, which can make a huge difference in risk during the procedure.
To control noise, a steam exhauster/silencer is used. In addition, temporary piping from the temporary steam turbine exit is used with a water injection point along the temporary pipe. This reduces both the temperature and the noise of the steam exciting the silencer.
Controlling noise and limiting temperature fluctuations is very straightforward when using the continuous blowing method. In continuous blowing, there is one continuous, low-pressure blow performed around the clock at a steady temperature and pressure.
Is steam blowing safe to perform on combine-cycle plants?
Steam blows can be safe to perform on combined cycle plants when properly planned and engineered. Specific considerations we make sure to cover when planning a combined cycle steam blow include:
- Establishing the correct number of stages to ensure each OTSG, HRSG and section of piping is addressed with the correct pressure.
- Minimizing water requirements to avoid expensive temporary water-sources to be brought on-site if possible.
- Thermal cycle planning for the fastest dislodging of mill-scale and debris with periodic cool downs during blowing.
- OTSG and HRSG feed rates are planned to correctly control steam flow during blowing.
- Additional piping (more than normal) for sound control is often required during combined cycle blows, so we ensure this is engineered into our plans as well.
Read more details about planning combined cycle steam blows here
When should I use air blowing vs. steam blowing?
Air blowing works in great combination with chemical cleaning, such as in power plant systems. The chemical cleaning solution will dissolve mill scale, and then the non-soluble particles that have been dislodged during cleaning can be removed via air blowing. Air blowing puts less direct stress on your system than steam blowing does, so if a chemical clean will be sufficient to remove mill scale, it is easier on your system to combine it with air blowing.
Read more about the pros and cons of each method here
OCI Methanol Beaumont: Plant restart and upgrade. Continuous steam blows, oil flushing, line blowing and chemical cleaning.
Longview Power Station Maidsville, WV – New Coal fired power plant – RIG performed chemical cleaning of the Boiler and Pre-boiler piping systems and performed impulse steam blows.
Jaguar Coal Fired Power Plant – 2 blocks Coal Fired Boilers- Performed chemical cleaning of the boilers. Hydrolazing on Steam, CCW, BFW and Condensate piping. Impulse steam blows.
Air Products Tees Valley Waste to Energy UK – RIG performed chemical cleaning of the HRSG’s, Hydrolazing of the Piping, Oil flushing of the CT’s / STG and steam blows of the headers and to the STG.
Hines Power Block Progress Energy Lakeland, FL – Chemical Plant Commissioning Project- New Combined Cycle project- Nooter Eriksen HRSG’s, Westinghouse CT’s and STG-Performed citric acid chemical cleaning, hydrolazing of all steam piping, air blows on Block 2 and continuous steam blows on Block 3.
RIG’s Steam Blowing Procedure
A typical steam blowing project with RIG progresses as follows:
- During an initial call, we extract critical project specifications and key information from you
- One of our engineers performs a site walk down to thoroughly plan the steam blowing procedure including the number of exit points, type of blow, temporary piping requirements, and other engineered features of your specific system.
- Any recommended pre-blowing services such as chemical cleaning, hydraulic line testing, and plate checks are performed.
- Our team takes full responsibility for the blow, shipping all necessary equipment and running the job on-site. A typical steam blow follows one of two methods:
- Impulse / puffing steam blows
- Boiler pressure is slowly raised to a pre-calculated pressure level and firing rate is increased.
- The water level in the drum is brought slightly above normal because during blowing it will drop significantly.
- Impulse / puffing steam blows
- A low-pressure verification blow is performed to ensure proper system setup for temporary piping and anchors.
- Temporary piping is used from a temporary steam turbine exit with water injection along the pipe to help quench and reduce the volume of steam before it reaches the steam exhauster/silencer. The quenching reduces the noise level.
- Temporary valve is opened to blow through the superheater, main steam pipe, and temporary pipe.
- Additional rounds of high-pressure ‘puffs’ are sent through the system. Steam blows are conducted without target plates until steam color becomes clear. Then preliminary target or impact plates are placed to capture particles going with the steam. RIG impulse steam blow uses the latest in fast opening hydraulic actuated valves that are hard surface coated to withstand debris and repeated opening and closing.
- While blowing, the boiler fire is put out and pressure is dropped, ensuring proper temperature differential to dislodge any adhering material.
- Steam blowing valve is closed and boiler is started.
- Final target plate of turbine blade is placed once preliminary target plate is in acceptable form.
- Blowing continues until indentations are acceptable as per turbine manufacturer guidelines.
- After mainstream line is complete, other stages are done in the similar fashion.
- Low pressure continuous blowing
- The process for continuous blowing is similar to the impulse blow method, but steam is produced by the boiler or heat recovery system generator and then allowed to escape through a temporary exit into piping.
- Additionally, pressure and temperature is continuously maintained during this method, which is easier on plant equipment
- The drawback to this method is that it is not quite as effective as the impulse method at removing debris because piping does not expand and contract as much, which can be key to dislodging some contaminants.
- Once the appropriate steam blow has been performed, we verify cleanliness levels with a visual inspection
- Temporary set-ups are then dis-assembled and full project documentation is turned over to you
Our team of pre-commissioning service experts ensures a safe and effective steam blow at your facility by creating a thorough work plan and documenting all potential hazards before the blow begins. We pre-plan, monitor, and track every detail to make sure no unnecessary thermal stress or pressure is used on your system, boiler, or sensitive equipment.
What is steam blowing?
It is the blowing of steam through piping to remove debris from the pipe, cleaning steam lines to a steam turbine, cleaning plant expansion lines, or new installs. As the definition says, to steam blow a pipe requires steam to blow through the pipe. This pipe can be attached to a boiler or heat recovery steam generator, and the other end of the pipe can be attached to a steam turbine.
Are there different types of steam blowing?
Yes, there are two main types of steam blow.
Continuous low-pressure steam blow: Steam is produced by the boiler or heat recovery steam generator and sent down the steam line piping at high velocity. The low-pressure method allows for a continuous steam pressure and temperature on the permanent plant equipment. The required steam blow is pre-calculated to use about 45 to 55% of the maximum design steam flow but at a low pressure. The low pressure upstream in the piping will be the back pressure of the permanent piping plus the temporary piping to the silencer. This method relies on high velocity, low density steam to clean the piping as opposed to the steam during operation which is low velocity, high density, and high pressure.
Impulse steam blows: The accepted method for a steam blow per NEMA 23 and NEMA 24 is an impulse blow where steam is pressurized in the boiler and released rapidly by opening a block valve. A break out point at the steam turbine is established and a quick opening valve is attached to this break out and a short piece of pipe is attached to vent the steam in a safe direction.
What types of silencers do you use?
Dry silencers are utilized where no personnel will come in contact with the temporary piping, the temporary piping is at full exit temperature, this will require the craft people to be quarantined from the area where the steam piping will be routed.
Water injection type silencers do require injection of water down stream of the permanent piping tie-in, as a result the temporary piping temperature is reduced dramatically. This is the safest application for congested work areas that will contain craft personnel.
How long does a steam blow procedure take?
The length of a steam blow varies depending on the specifics of the system being cleaned (pipe lengths, number of exit points, etc), however an average steam blowing project can take around 2 weeks. To shorten this timeline, hydrolazing before a steam blow can shave 5-8 days off the steam blow.
Continuous steam blows can usually be completed much faster than an impulse steam blow. An impulse steam blow takes many valve cycles to exhaust the steam at a good cleaning force ratio for only short sections at a time, whereas, during a continuous steam blow the steam is always flowing and the cleaning force ratio becomes greater down the line as the pressure drops towards the exit.
What regulations do you follow during steam blows?
Generally when the piping is attached to a steam turbine the steam turbine manufacturer has already developed a guideline as to how this piping must be steam blown. There are several general methods already established to complete this and of these NEMA 23 and NEMA 24 are two of the guidelines generally referenced. These are general guidelines and Section 8 of each NEMA procedure is identical as to method and purpose of the steam blow.
How do you reduce noise and high temperatures during steam blowing?
One basic precaution includes using dry silencers that don’t require water injection to reduce noise, which can make a huge difference in risk during the procedure.
To control noise, a steam exhauster/silencer is used. In addition, temporary piping from the temporary steam turbine exit is used with a water injection point along the temporary pipe. This reduces both the temperature and the noise of the steam exciting the silencer.
Controlling noise and limiting temperature fluctuations is very straightforward when using the continuous blowing method. In continuous blowing, there is one continuous, low-pressure blow performed around the clock at a steady temperature and pressure.
Is steam blowing safe to perform on combine-cycle plants?
Steam blows can be safe to perform on combined cycle plants when properly planned and engineered. Specific considerations we make sure to cover when planning a combined cycle steam blow include:
- Establishing the correct number of stages to ensure each OTSG, HRSG and section of piping is addressed with the correct pressure.
- Minimizing water requirements to avoid expensive temporary water-sources to be brought on-site if possible.
- Thermal cycle planning for the fastest dislodging of mill-scale and debris with periodic cool downs during blowing.
- OTSG and HRSG feed rates are planned to correctly control steam flow during blowing.
- Additional piping (more than normal) for sound control is often required during combined cycle blows, so we ensure this is engineered into our plans as well.
Read more details about planning combined cycle steam blows here
When should I use air blowing vs. steam blowing?
Air blowing works in great combination with chemical cleaning, such as in power plant systems. The chemical cleaning solution will dissolve mill scale, and then the non-soluble particles that have been dislodged during cleaning can be removed via air blowing. Air blowing puts less direct stress on your system than steam blowing does, so if a chemical clean will be sufficient to remove mill scale, it is easier on your system to combine it with air blowing.
Read more about the pros and cons of each method here