MHC Flushing & EHC Flushing Services
Turbines are especially sensitive to bacterial growth and other contaminates and they are not easy to service. Our certified technicians have serviced turbines around the world with our RIG team EHC flushing services that are designed specifically for sensitive electro-hydraulic controlled equipment.
We address the most common causes of turbine downtime including contaminates hiding in the turbine trip and monitoring system. Our filtration systems are designed for use on phosphate ester fluids and include viton seals. We have performed MHC flushing services at power plants and combined cycle plants around the US and the world and would be happy to provide our trusted, turnkey services at your plant.
800-770-4510 (Domestic)
+1 281-339-5751 (International)

Power Plant EHC Flushing Services Fluid Swap
Switching from a vegetable-based ester to a polyalkylene glycol EHC lubricant was proving challenging for a power plant because of the incompatibility of the two fluids. The replacement fluid (polyalkylene glycol) needed to contain less than 3% total volume of the existing fluid at the end of the project.
Power Plant GE Turbine HVOF & MHC Flushing
RIG was contracted to perform a high velocity hot oil flush of the General Electric turbine at a Power Plant in Indianapolis, IN. Our technicians arrived onsite on 12/12/17, completed site specific safety training, and conducted a safety walk down of the work area.
Turbine HPT5 Bearing Resolution & Flushing
RIG was contracted to provide services after a different flushing provider left a flange slip screen in place in front of turbine’s HP T5 Bearing. Flushing procedures did not list the inspection point or verification of removal. The screen, plugged with contamination, starved the bearing of oil and caused $1.2M in damage and downtime.
RIG’s electro-hydraulic controlled (EHC) flushing services include:
- Turkey flushing solutions developed by our engineering team that:
- Specify which equipment we will use on-site, including
- Jumper cable installations
- Critical flow paths and any additional piping setups
- Auxiliary filtration units
- Industrial filters and breathers
- Flanges and other equipment
- Defines cleaning chemicals and flow paths, including entry paths and filter placement and includes pipe fitting support for breakdown and re-installation of all piping components
- Establishes current cleanliness levels and the improved ISO numbers we will achieve. We always provide:
- Continuous fluid analysis onsite during the flush using our field Laswer Particle Counter
- Third-party confirmation of final particle counts within 24 hours of job completion
- Specify which equipment we will use on-site, including
We also offer additional service add-ons for improved system performance, including:
- Side stream filtration during the flushing process
- Varnish removal
- Reservoir and tank cleaning
- And other reliability services as needed
Overview of EHC Flushing Steps
- Our team extracts project specifications from you and then schedules a walk down of your plant
- At the completion of our on-site visit, a complete flushing plan is developed including piping specifications, flow paths, instrumentation and equipment specifications and target ISO cleanliness numbers for your review
- Once the project begins, we verify current contamination levels and setup all equipment
- Our team takes full responsibility for on-site flushing, and usually completes flushes within 4-7 days.
- After flush completion, we provide full documentation of steps completed and results, including independently verified contamination levels
As a leading hot oil flushing company, we have performed numerous turnkey lube oil flushing services on both gas turbines and steam turbines made by:
- GE
- Siemens–Westinghouse
- Dresser–Rand
- Elliot
- Kobelco
- Sulzer
- Solar Turbines (CAT)
- And more…
Don’t see your turbine listed? Chances are we have worked with your equipment or something very similar. Give us a call to talk to us specifically about your needs and verify RIG can do the job.
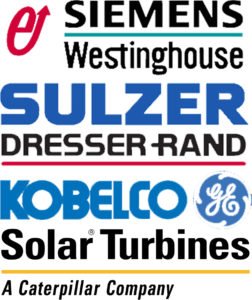
Switching from a vegetable-based ester to a polyalkylene glycol EHC lubricant was proving challenging for a power plant because of the incompatibility of the two fluids. The replacement fluid (polyalkylene glycol) needed to contain less than 3% total volume of the existing fluid at the end of the project.
RIG was contracted to perform a high velocity hot oil flush of the General Electric turbine at a Power Plant in Indianapolis, IN. Our technicians arrived onsite on 12/12/17, completed site specific safety training, and conducted a safety walk down of the work area.
Turbine HPT5 Bearing Resolution & Flushing
RIG was contracted to provide services after a different flushing provider left a flange slip screen in place in front of turbine’s HP T5 Bearing. Flushing procedures did not list the inspection point or verification of removal. The screen, plugged with contamination, starved the bearing of oil and caused $1.2M in damage and downtime.
RIG’s electro-hydraulic controlled (EHC) flushing services include:
- Turkey flushing solutions developed by our engineering team that:
- Specify which equipment we will use on-site, including
- Jumper cable installations
- Critical flow paths and any additional piping setups
- Auxiliary filtration units
- Industrial filters and breathers
- Flanges and other equipment
- Defines cleaning chemicals and flow paths, including entry paths and filter placement and includes pipe fitting support for breakdown and re-installation of all piping components
- Establishes current cleanliness levels and the improved ISO numbers we will achieve. We always provide:
- Continuous fluid analysis onsite during the flush using our field Laswer Particle Counter
- Third-party confirmation of final particle counts within 24 hours of job completion
- Specify which equipment we will use on-site, including
We also offer additional service add-ons for improved system performance, including:
- Side stream filtration during the flushing process
- Varnish removal
- Reservoir and tank cleaning
- And other reliability services as needed
Overview of EHC Flushing Steps
- Our team extracts project specifications from you and then schedules a walk down of your plant
- At the completion of our on-site visit, a complete flushing plan is developed including piping specifications, flow paths, instrumentation and equipment specifications and target ISO cleanliness numbers for your review
- Once the project begins, we verify current contamination levels and setup all equipment
- Our team takes full responsibility for on-site flushing, and usually completes flushes within 4-7 days.
- After flush completion, we provide full documentation of steps completed and results, including independently verified contamination levels
As a leading hot oil flushing company, we have performed numerous turnkey lube oil flushing services on both gas turbines and steam turbines made by:
- GE
- Siemens–Westinghouse
- Dresser–Rand
- Elliot
- Kobelco
- Sulzer
- Solar Turbines (CAT)
- And more…
Don’t see your turbine listed? Chances are we have worked with your equipment or something very similar. Give us a call to talk to us specifically about your needs and verify RIG can do the job.
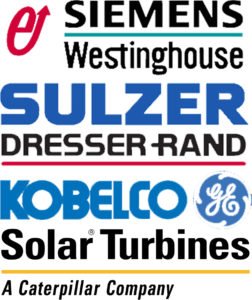