Hydrostatic Pipe Testing Services
The RIG team provides hydrostatic testing services to test the integrity of your pressure equipment. Before being placed into service any pressurized equipment is required to be pressure tested. Examples of equipment requiring hydrotesting testing services are:
- Process Piping
- Pipelines
- Boilers
- Heat Recovery Steam Generators
- Pressure Vessels
- Storage Tanks
Each type of equipment is subject to specific codes and inspections before it is placed into service. RIG will work with you to ensure the hydrostatic pipe testing process is executed safely and to the correct standards. Complete and accurate documentation will be produced and handed over to the required parties.
Our team of certified technicians can respond rapidly to your request to provide equipment and perform hydrostatic testing. Safety and quality are at the forefront during hydrotesting activities. All hydrostatic tests performed by our team include a hydrotest tree with a certified gauge and relief valve to prevent over pressurization of the equipment. RIG is a leader in pipeline hydrostatic testing companies and has the experience and capability to perform hydrotests with unique requirements, for example RIG can provide heating and circulating equipment to test HRSGs when minimum metal temperatures must be achieved during the hydrotest.
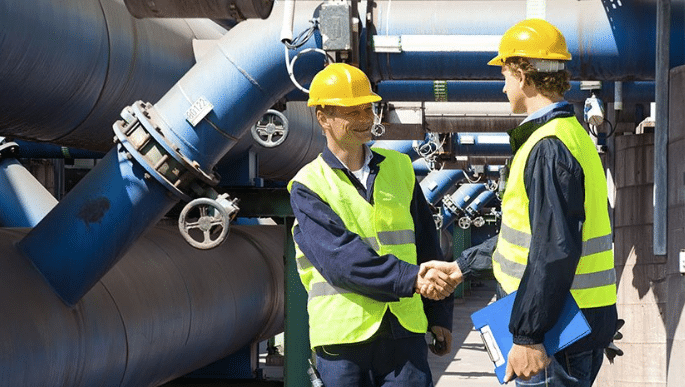
800-770-4510 (Domestic)
+1 281-339-5751 (International)
Hydrotesting and chemical cleaning of the boilers, fuel oil piping and condensers. Hydrolazing on Steam, CCW, BFW and Condensate piping. Oil flushing of 2 SKODA STG’s. Impulse steam blows of 2 blocks of SKODA STG’s.
Provided High Velocity Oil Flushing (HVOF) on Dresser Rand reciprocating compressors, and pressure testing and high pressure flushing of the Tiger West Rail Hydraulic system
2 Blocks Coal Fired Boilers- Chemical cleaning and pressure testing of the boilers. Hydrolazing on Steam, CCW, BFW and Condensate piping. Impulse steam blows.
New coal fired power plant – chemical cleaning of the boiler and pre-boiler piping systems, hydrotesting, and impulse steam blows
What is hydrostatic testing services?
A hydrostatic test is a way in which equipment such as pipelines, boilers, pressure vessels, and tanks can be tested for strength and leaks by pressurizing the system with water. Hydrostatic testing is the most common method employed for verifying the integrity of piping and pressure equipment.
What are the steps to performed by hydrostatic testing companies?
Each type of equipment will be subject to a specific procedure. An overview of the generic steps involved in hydrotesting are:
- Fill the vessel or pipe system with a liquid, usually water, and ensure all air is vented out of the system.
- Pressurize the system to the appropriate test pressure (calculated in advance based on system design details).
- Test the pressure tightness by isolating the liquid supply valve and observing whether there is pressure loss.
- Identify the location of a leak through visual inspection.
- Hold the system at test pressure for a predetermined period of time once system is confirmed to be leak free.
- Upon completion of a successful test, drain the system and complete all required paperwork and test certificates.
Why should hydrotesting be performed on a regular basis?
Using this test helps maintain safety standards and ensure the integrity of a vessel over time. Newly manufactured equipment is initially qualified using the hydrostatic pipe testing. It is then re-qualified at regular intervals using the proof pressure test which is also called the modified hydrostatic test. Periodic testing of pressure vessels for transport and storage of gases is very important because such containers can explode and cause serious damage, injury, and environmental contamination if they fail under pressure.
What codes do pressure vessels have to meet?
Pressure vessels, boilers, HRSGs, and piping systems are tested to the accepted ANSI code depending on the plant they are in. This code is B31.3 for chemical plants and refineries, and B31.1 for power plants. For boilers and HRSGs, the test must conform to boiler codes applicable in the state where the equipment is located. There are additional codes for onshore and subsea pipelines.
What is the difference between hydrotesting and pneumatic testing?
Hydrotesting is performed with a liquid, usually water, and requires that the system be able to accommodate the fluid. This means that the system must be able to support the weight of the test fluid and won’t be contaminated by the fluid. Pneumatic testing is performed using a gas, usually air or nitrogen, to pressurize the system. Pneumatic testing carries a significant safety risk in that the stored energy of the pressurized fluid is extremely high. Should any system component fail during the test the resulting damage could be catastrophic. Pneumatic testing is used in very specific situations where hydrotesting is not feasible. It is important that the pneumatic test is correctly engineered, approvals received from the relevant authorities, and performed safely. Speak to an experienced RIG representative about your specific situation.
Hydrotesting and chemical cleaning of the boilers, fuel oil piping and condensers. Hydrolazing on Steam, CCW, BFW and Condensate piping. Oil flushing of 2 SKODA STG’s. Impulse steam blows of 2 blocks of SKODA STG’s.
Provided High Velocity Oil Flushing (HVOF) on Dresser Rand reciprocating compressors, and pressure testing and high pressure flushing of the Tiger West Rail Hydraulic system
2 Blocks Coal Fired Boilers- Chemical cleaning and pressure testing of the boilers. Hydrolazing on Steam, CCW, BFW and Condensate piping. Impulse steam blows.
New coal fired power plant – chemical cleaning of the boiler and pre-boiler piping systems, hydrotesting, and impulse steam blows
What is hydrostatic testing?
A hydrostatic test is a way in which equipment such as pipelines, boilers, pressure vessels, and tanks can be tested for strength and leaks by pressurizing the system with water. Hydrostatic testing is the most common method employed for verifying the integrity of piping and pressure equipment.
What are the steps to performing a hydrostatic testing procedure?
Each type of equipment will be subject to a specific procedure. An overview of the generic steps involved in hydrotesting are:
- Fill the vessel or pipe system with a liquid, usually water, and ensure all air is vented out of the system.
- Pressurize the system to the appropriate test pressure (calculated in advance based on system design details).
- Test the pressure tightness by isolating the liquid supply valve and observing whether there is pressure loss.
- Identify the location of a leak through visual inspection.
- Hold the system at test pressure for a predetermined period of time once system is confirmed to be leak free.
- Upon completion of a successful test, drain the system and complete all required paperwork and test certificates.
Why should hydrotesting be performed on a regular basis?
Using this test helps maintain safety standards and ensure the integrity of a vessel over time. Newly manufactured equipment is initially qualified using the hydrostatic test. It is then re-qualified at regular intervals using the proof pressure test which is also called the modified hydrostatic test. Periodic testing of pressure vessels for transport and storage of gases is very important because such containers can explode and cause serious damage, injury, and environmental contamination if they fail under pressure.
What codes do pressure vessels have to meet?
Pressure vessels, boilers, HRSGs, and piping systems are tested to the accepted ANSI code depending on the plant they are in. This code is B31.3 for chemical plants and refineries, and B31.1 for power plants. For boilers and HRSGs, the test must conform to boiler codes applicable in the state where the equipment is located. There are additional codes for onshore and subsea pipelines.
What is the difference between hydrotesting and pneumatic testing?
Hydrotesting is performed with a liquid, usually water, and requires that the system be able to accommodate the fluid. This means that the system must be able to support the weight of the test fluid and won’t be contaminated by the fluid. Pneumatic testing is performed using a gas, usually air or nitrogen, to pressurize the system. Pneumatic testing carries a significant safety risk in that the stored energy of the pressurized fluid is extremely high. Should any system component fail during the test the resulting damage could be catastrophic. Pneumatic testing is used in very specific situations where hydrotesting is not feasible. It is important that the pneumatic test is correctly engineered, approvals received from the relevant authorities, and performed safely. Speak to an experienced RIG representative about your specific situation.